Machinery maintenance – top tips for winter
Here in the northern hemisphere winter means machinery maintenance. With less mowing the workshop will now be busier with annual servicing and checks to make sure each and every machine is running to the best of its ability. Even more so for machinery needed in the field during the harder, harsher mowing conditions that winter brings.
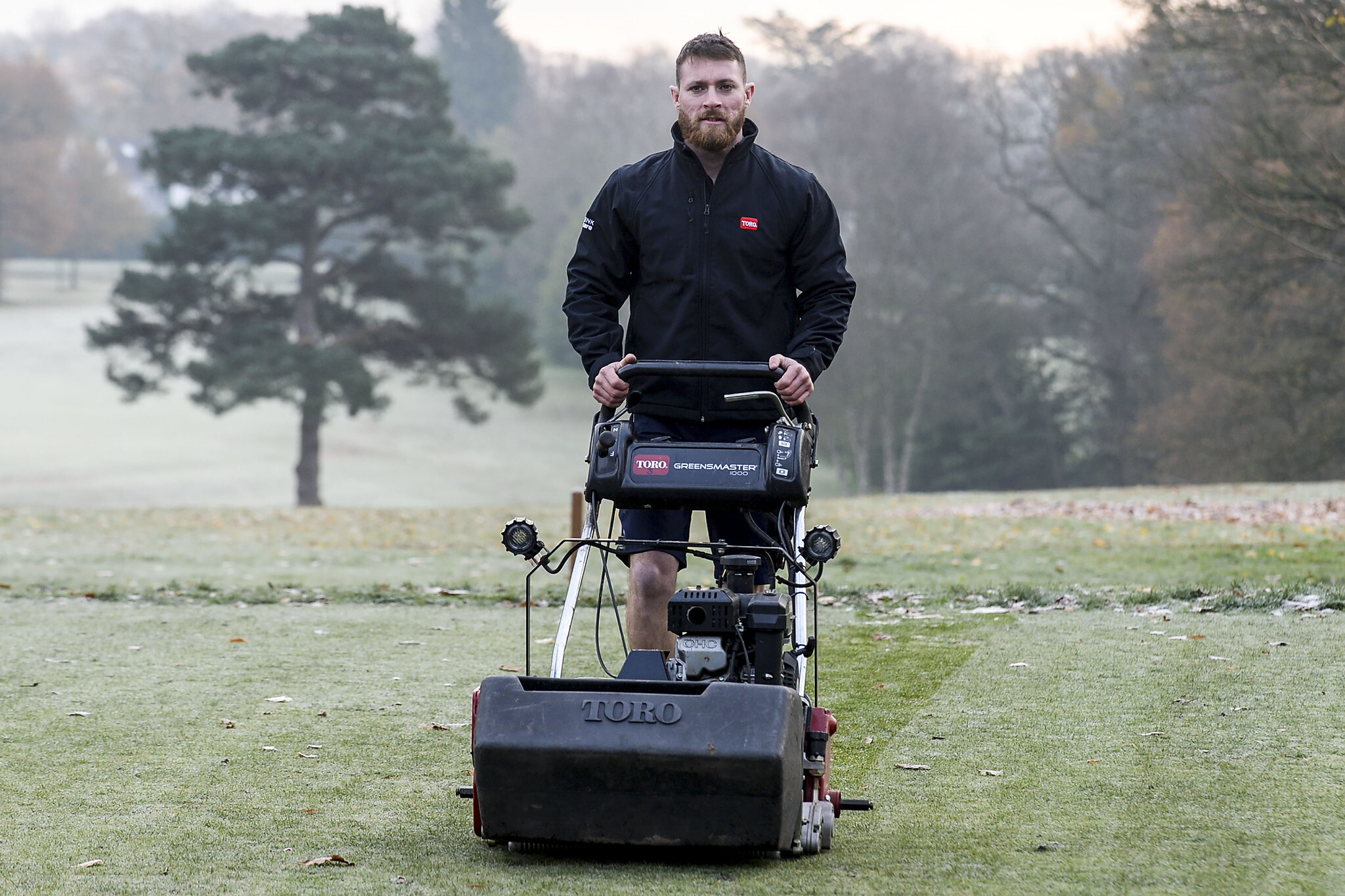
Here Michael Hampton, Turfcare Parts Manager from Reesink Turfcare, UK distributor of Toro fine turf and groundscare machinery and Toro Parts, considers what needs to be done to ensure your machines are quickly back functioning to their full capabilities following a long tough season.
While getting machinery ready for the coming season can seem daunting, keeping surfaces in play and well maintained throughout winter is also tough. Good maintenance will ensure your machines are functioning to their full capabilities whatever the time of year or weather conditions, and the fact is that planned winter maintenance is considerably cheaper than ad-hoc repairs during the season.
And whether machinery maintenance in the busy mowing season has been done like clockwork or in a need-to only manner, the last thing needed in the harsh winter months is downtime due to not having the right parts or having not been vigilant with maintenance. Now is either the time to catch up or have a full pre-spring clean.
Most machines will be out at some point over winter, there’s no total shut down, but cold weather issues and extended periods of time between use will affect the machines. Seized breaks and motors spring to mind as the most common.
During a recent chat with course manager Kim Kirkham at Sherwood Forrest Golf Club, who has been at the club for almost 40 years, he revealed winter maintenance is a vital part of their greenkeeping calendar. He says with cutting in the winter months going down to three times a week it is a good time to strip back the machines and take an in-depth look at the oil and grease points in particular and take the opportunity to inspect and sharpen blades. For blade inspection best practices see the figure below.
Sherwood’s workshop puts the greens machines first in terms of priority, simply for the fact that they are out every day and being used the most mean they require a little bit more TLC than the “more manly” fairway mowers!
First up is a thorough steam clean. Grass gets everywhere and if left will cause rust so it’s important to get it all off after every use and even more important when there are longer periods between use. This gives absolute visibility to any potential problems and makes way for the machines’ annual “MOT”.
When everything is spotless it’s time for a thorough inspection of the things Kim highlights, and more – the engine and hydraulics, tyres, filters and brakes can all be assessed at this point.
Preventative maintenance especially on the machine’s engine is very important. Not only does it get rid of potentially harmful dirt but gives the chance to check for leaks, loose parts and damaged components. Take the opportunity to replace anything that’s damaged and tighten anything that’s loose.
No matter how tempting, don’t clean the engine with a pressure washer, this can cause damage to the seals. Instead, when cool, spray the engine with a non-petroleum degreaser, wait for this to start breaking down and then wipe clean. Warm water at a low pressure can be used but always make sure the engine is dried thoroughly after.
Batteries can often be overlooked in terms of maintenance, but at your peril. They are usually covered in dirt, grass clippings and moisture and all this, if left, can lead to corrosion. So it is essential if things in this area have been overlooked in the busy months, that they are dealt with over winter.
Look for oil leaks. Oil should be changed at least every 100 hours anyway to remove potentially harmful sludge; similarly, regardless of how dirty they are air filters should be changed every 100 hours too. Along with the oil, the air filter is one of the most important factors in promoting peak performance and long service life and winter maintenance doesn’t much differ to these good practice maintenance techniques, but it does provide a good opportunity to remind ourselves of the best ways to check them.
Clean air is essential to keep your engine smoothly and efficiently. In fact inadequate air filtration can cause more harm to your engine than poor lubricant filtration, but when it comes to best practices it can get a bit tricky. For example, don’t remove an air filter from its housing simply to inspect it. Removing and replacing it can cause dirt from the gasket sealing surface to drop on the clean filter side when the gasket is released. Other top tips here, please see the figure below, are: never hit a filter to clean it (rapping hard enough to knock the dust off damages the filter) and never leave the air filter open longer than necessary (this provides contaminants smaller than the eye can see direct entry into the engine).
Routine greasing and keeping cylinders good and sharp are obvious maintenance priorities. Knowing whether cylinders are ready for a replacement is simple. The ‘paper test’, which involves running a strip of paper through the cutting unit, will indicate if you’re cutting to the best of your machine’s ability. If it produces a clean cut, your cylinders are fine, if it’s anything less than perfect, it’s time to regrind or replace.
A full post-clean grease-up for all the joints and moving points puts the ‘goodness back in’ and an all-over blast of maintenance lubricant acts like a film to help prevent any issues when the machines are being pushed hardest during difficult conditions.
When the machine is completely clean, it’s a good time to assess if there’s anywhere needing a paint touch-up to prevent rusting. You’ll also identify things – a chafing hose for example or weeping coupling which may have gone unnoticed under a coat of dried clippings. Dealing with these sorts of things immediately means reliability is increased.
It’s good to be organised when it comes to maintenance. Hard ground conditions means machines are working harder than ever and that can mean replacement parts are more regularly needed. Rather than experience downtime waiting for parts it’s advisable to keep a stock in the workshop. Opt for filters, bedknives and bearings if space is limited as these are what are most often needed.
A constant focus on machinery innovation has seen turf machinery improve over the years in terms of productivity, fuel and energy efficiency and emission reduction. This includes those machines powered by propane, hybrid, advanced battery, electronic fuel injection and LED technologies. And no matter how talented the workshop team, there will be some machines featuring intelligent electronic systems and advanced engine management systems such as Toro’s Smart Power and GeoLink GPS that will most likely need checking over by a trained dealer. These sorts of diagnostic checks and software tweaks can be scheduled at fixed service intervals, but all other maintenance is best done regularly, with planned winter servicing scheduled in advance. If you have the resource to do this in-house all-the better.
But not every club is in possession of a workshop manager or workshop or team with the know-how or time to take this sort of job on. And that’s where dealers and service centre support steps in. Book in a mid-season service and, as the saying goes, they’ll do the hard work for you.
Doing this year in, year out and keeping on top of general maintenance ensures your machines are in the best possible condition. It can be tempting to cut corners when it comes to servicing and it can be expensive to make repairs, but well-maintained kit tends to be trouble-free and the age-old saying rings true that prevention is better than cure, especially when trying to make sure maintenance costs stay within budget.